How To Service Your Aqua-Hot Hydronic Heating System
A Do-It-Yourself Guide to Keeping the Diesel Burner Running
Article Date: April, 2010
Article and Photography by Mark Quasius
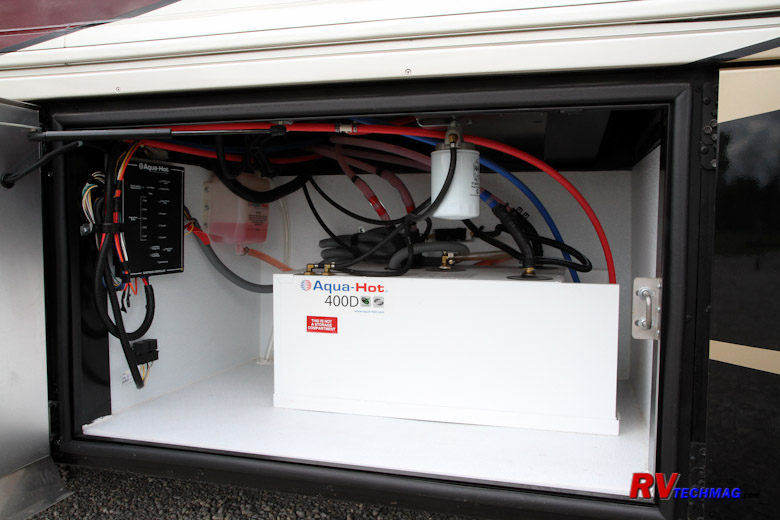
Hydronic heating systems are very popular in upper scale class A motorhomes. A hydronic heating system utilizes a
diesel burner and an electric heating element to heat a boiler, that then circulates boiler antifreeze throughout various zones within the
coach to provide heating via small heat exchangers. In addition domestic hot water heating needs are also met by the hydronic heating systems.
The most prevalent system used in RVs is made by Aqua-Hot Heating Systems, formerly
known as Vehicle Systems, Inc. Previous models went by the name of Hydro-Hot whereas current models are named Aqua-Hot. The
basic design is identical so for all practical purposes, whenever I refer to Aqua-Hot, I am also including the units badged as Hydro-Hot and
the terms are interchangeable for the intents of this tutorial. This tutorial is not meant to detail the basic operation of hydronic heating
systems. That information is best viewed in the RV Tech Library.
This tutorial is directed to owners of Aqua-Hot systems that want to perform their own basic diesel burner service work.
The diesel burner on your Aqua-Hot does require occasional service work, generally recommended on an annual basis. This
service interval can vary, depending on just how much you use your hydronic heating system. Servicing the burner isn't all that hard to do once
you know the basic steps. It can be time consuming and having this work done by a service professional will cost you some money, which is mostly
for their labor, not for the service parts used. If you want to do your own burner service, read on. I'll take you through the basic steps that
I use when servicing my diesel burner. If you still want to perform your own service be sure to refer to the proper service manual for your unit
to view the exact specs and procedure for your particular model. The service manual for my particular model can be found at
This Link. However, the Webasto burner that is used in these models is virtually identical
so yours should be similar, if not identical. In addition, I'll also detail a few modifications I made to my system to make it easier to service.
These mods have drastically reduced the time spent on future service procedures as well as corrected a few deficiencies in the system. These mods
are probably more specific to my model and year of Allegro Bus so many of them will not apply to your coach.
Performing your own maintenance isn't that hard. In the following paragraphs I'll try to walk you through the steps I take
to perform basic service work on my burner. It's not a complete troubleshooting guide nor does it cover electrical component testing or
troubleshooting. For that, please refer to the service manual in the previously mentioned link. This work is being performed on my 2007 Allegro
Bus 42QRP.
Getting Started
Before we start we have to wonder what this annual service really is. Basically, it's replacing the fuel filter, replacing
the burner nozzle, and giving the burner a good inspection. If anything is found out of tolerance it can be corrected at this time. If the
combustion chamber is sooted up, it can be cleaned at this time. If things are running well on your system all you'll probably have to do is
change the fuel filter and replace the burner nozzle. Aqua-Hot recommends an annual burner service. However, many field service techs agree that
if the unit is burning fine, leave it alone. The annual recommendation is based upon average use. After so many gallons of diesel fuel have run
through the fuel filter it will need replacement. Again, this will vary as to how clean your fuel was. The burner nozzle is a finely machined
orifice that is designed to spray fuel at a 60 degree cone and at a flow rate of .35 gallons per hour. This hole will erode over time just from
passing fuel through it. The more fuel that passes through it, the greater the erosion. When the hole increases in size your fuel flow rate will
increase, resulting in a burner that runs rich, develops an unburned fuel odor, and may even smoke. If you don't run your heating system that
often there may be no need to change the nozzle on an annual basis. Conversely, if you use your system extensively you may need to perform this
service more frequently. Remember that this service should be done as needed, not just because a piece of paper has one year printed on it.
However, the annual service interval is a good average for many RVers.
Okay, assuming that we have determined that it's time to service our diesel burner, let's consider what we need. First of
all, we'll need some parts. A fuel filter and replacement nozzle should be in hand prior to turning any wrenches. The .35 burner nozzle is small
compared to nozzles used in home heating applications so you are not going to find this item at your local heating supply house or home
improvement store. You may find it at a local RV dealer who performs service work on hydronic heating systems or else you can order it direct
from Aqua-Hot Heating Systems. The fuel filter can vary between various models. In my case it was a Garber spin-on fuel filter. This unit was
available from Aqua-Hot or from an RV dealer but I also was able to match it to a Wix # 31099. You'll also need some tools. A couple of Phillips
head screws hold the cover onto the unit. A 3/8" drive ratchet with a 10" long extension (or a 6" and 4" coupled together) and a 10mm deep well
socket will be needed to remove the burner from the unit. A 5/8" and 3/4" wrench will be needed to remove the nozzle and an oil filter wrench is
needed to remove the fuel filter. Various other tools may be needed as required but the items listed are the bare minimum that you'll need. If
you want to do more work or testing you may need a voltmeter, fuel pressure gauge, etc. A brush will be needed in order to clean out the burner
if it's sooted up and a vacuum or air hose to blow the loose soot out or suck it up. Naturally, a copy of the service manual is indispensable to
refer to when checking tolerances, voltages, etc.
Changing the Fuel Filter
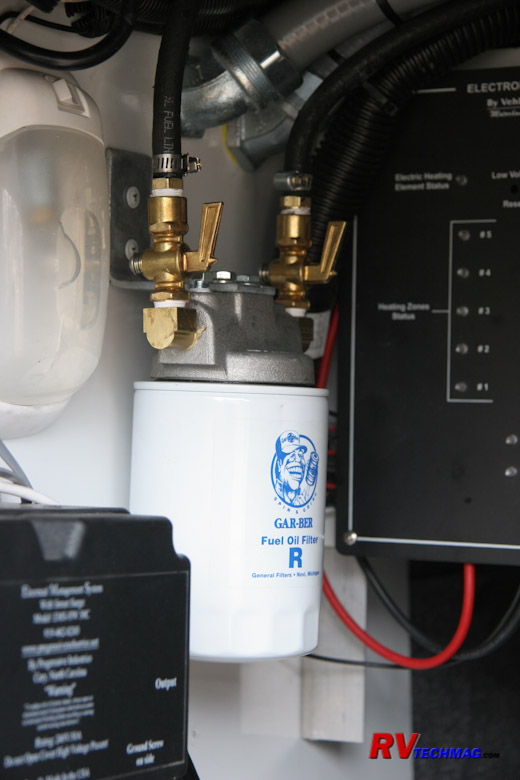
The first thing to do is to replace the fuel filter. Most systems use the Garber spin-on fuel filter which can easily be
removed with a standard oil filter wrench. There is an o-ring seal on the filter housing threads. A new one probably came with your filter so
replace it. If you do not have a new o-ring leave the old one on. Chances are there's nothing wrong with it. Be careful to not add a new o-ring
without first removing the old one or else they will stack up and your filter will not tighten properly. Prior to spinning on the new filter,
rub a little fuel oil on the gasket to prevent it from pinching and binding when you install the filter. The above image shows a pair of shutoff
valves that I have installed on my coach. Normally you won't have these on your coach unless you added them yourself. But, they help prevent the
dribbling and draining of fuel that is in the lines when the filter is removed. You can always use a vise grips pliers to pinch off the fuel
line to eliminate any drainage but adding these valves does make it much easier.
Purging the Air from the Fuel System
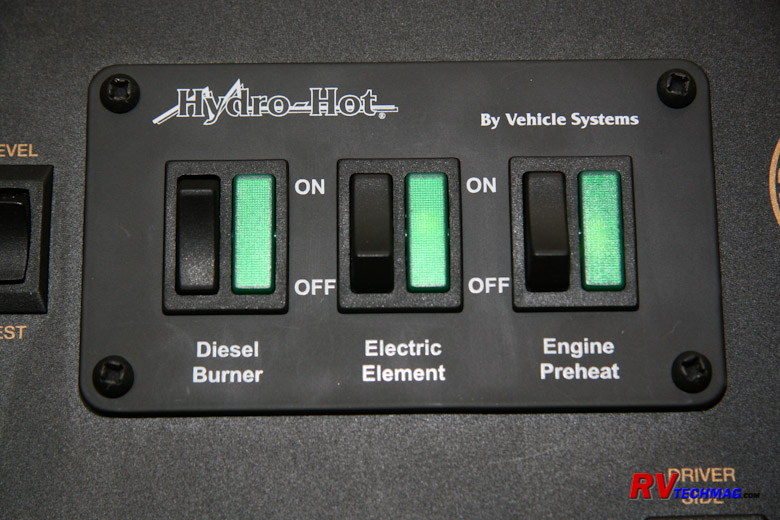
Now that the filter has been changed, you will need to purge the air out of the fuel system. When you switch on the diesel
burner, the burner will run for approximately 15-30 seconds. When the burner motor runs the blower runs as well as the fuel pump. This is a purge
cycle designed to blow air through the combustion chamber so that any hot spots can be cooled and any unburnt fuel can be purged. After the initial
purge time has passed the burner's electronic controller module will allow the fuel solenoid valve to open, and fuel will flow through the nozzle.
At the same time the transformer will energize, sending a high voltage current to the electrodes, which creates a spark, igniting the fuel. The
electrodes will stop sparking once the photocell determines that the burner has been lit. When it's time to stop heating the boiler, the fuel
solenoid will close and the burner flame will stop. The blower motor will continue to purge air through the combustion chamber for another minute
or two in order to cool down the unit. It's important to note that the electronic controller times and switches the various components within the
burn cycle but the fuel pump is constantly turning and pumping fuel whenever the blower is running. It's just not atomizing it through the nozzle
whenever the fuel solenoid valve is closed.
In order to purge the air from the fuel system, we just need to run the pump for a while. To do this switch on the diesel
burner. Allow it to run for 5-10 seconds to initiate the pre-burn purge cycle, and then switch it off. The burner will enter the post-burn purge
and cool down cycle and will continue to run for a minute or two. During this time the fuel pump will attempt to pump fuel and return it to the
fuel tank via the return line. If you listen carefully you will hear the motor sound change and bog down once the fuel finally gets to the pump.
You may have to repeat this cycle a second time if all of the air has not yet been purged from the lines. You will need to have all of the air
purged from the fuel lines if you want to test your burner's operation or check the fuel pump pressure. Once the filter is changed and the purge
complete, you can move on to tackle the burner itself.
Accessing the Burner Compartment
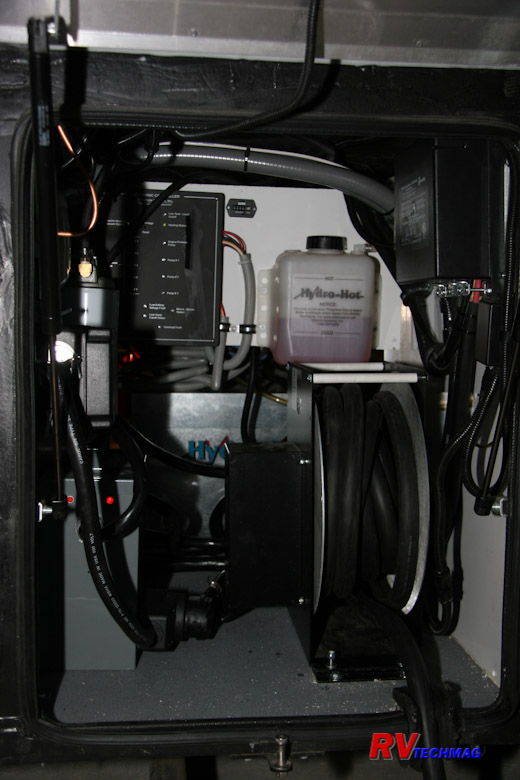
The above image shows what my Hydro-Hot compartment looks like. It's a mess isn't it? This is one of the reasons why labor
costs to service these units runs as high as it does. Just getting to the unit can take a sizeable amount of labor time. Originally there was a
central vacuum unit located in this bay. I removed it and relocated it to another location and used that space to place my Hughes Autoformer,
which can be seen in the left-forward location in this bay. The rear white board used to be much lower and encumbered access to the Hydro-Hot
burner. I removed the board and shortened it so that I could easily remove the sheet metal panel from the Hydro-Hot enclosure in order to access
the burner. I then rearranged the surge tank and controller panel and even added an hour meter to that panel because the original one was buried
on the top of the unit where it was impossible to see. Later on I even added a second switch for the diesel burner so that I didn't have to run
all the way back into the coach when servicing the unit, although this photo was taken prior to my addition of that switch.
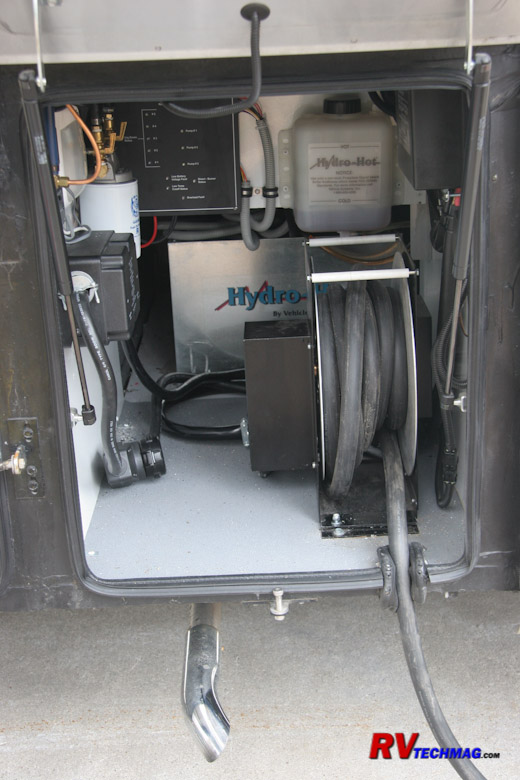
This image shows the same area with the Autoformer removed. I connected the Autoformer with plug-in connectors so that it
could easily be removed and/or bypassed if needed. The cord reel was also modified with quick disconnects on the 12 volt power to the cord reel
motor and I also fabricated some steel adaptor plates with studs. All I have to do is remove two 1/4" nuts, unplug the cord reel motor and lift
the cord reel assembly out of the bay. The sheet metal cover is then easily removed from the main unit to expose the burner.
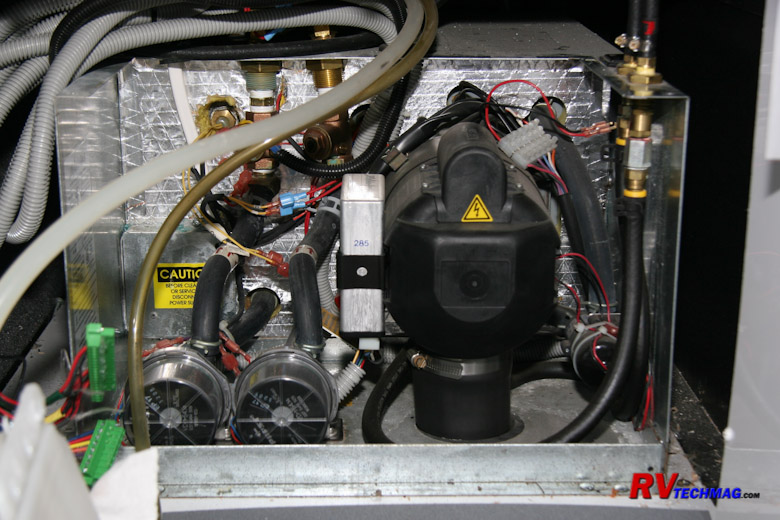
In this closer view the burner cover has been removed. Here we can see the fuel lines entering the unit at the top right.
One line is a supply line that comes from the fuel filter, which is connected to the fuel tank via a dedicated fuel pickup tube within the tank.
The second line is a return line that returns unused fuel to the fuel tank. The Webasto burner is a two pipe system that constantly pumps fuel
from the inlet to the return line and back to the tank. This is necessary to ensure bleeding any air out of the system after the tank has run dry
or the fuel filter has been changed. The large black item is the Webasto burner. This unit contains the burner motor, ignition transformer, fuel
pump, blower fan, fuel shutoff solenoid, nozzle, electrodes, and photocell sensor. All of this is stuffed into one compact unit. A silver
controller box is also visible in this image and is attached to the left side if the burner. This electronic controller module controls the burner
motor, fuel solenoid, ignition transformer, and photocell operations. It performs all of the timing and switching operations needed during the
purge and burn cycles. The two larger round items at the bottom-left are the circulating pumps for the anti-freeze and the 4" square electrical
box with the yellow warning label covers the 120 volt electric heating element. None of these have anything to do with burner service. Also, note
the hose clamp around the rubber hose at the bottom of the burner. This is a rubber air intake hose for the burner that extends through a hole in
the floor. It is designed to feed outside air to the burner for combustion purposes. It has a reputation for collapsing when operating, which
restricts the intake air to the burner and makes it run rich. It can be removed with no ill effects but the electrical wiring and components in
your housing are no longer shielded against any intrusion against field mice. Many owners remove the hose and then attach a piece of 1/4" wire mesh
screening over the hole to prevent this. In my case I just put some mesh inside the intake hose to prevent it from collapsing.
Removing the Burner
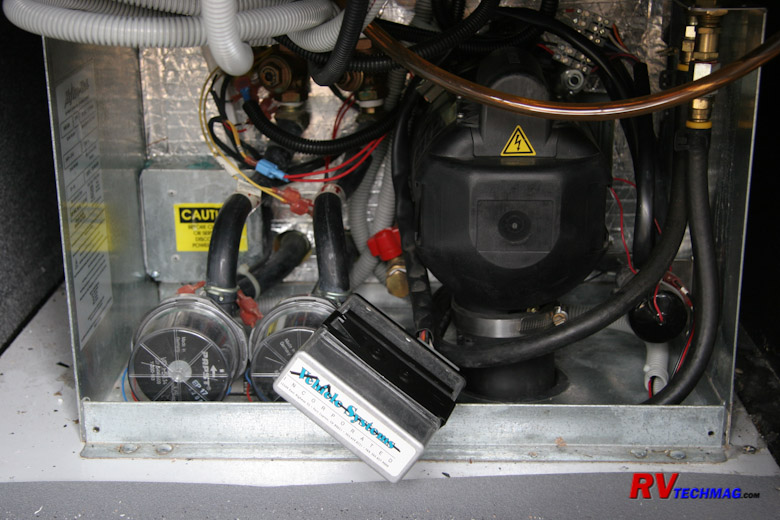
This image shows the electronic burner controller module removed from the burner. The module slides of the side of the burner
and the wiring harnesses can be unplugged to set it aside for better access. There are two wiring harnesses but their plugs are polarized and of
different sizes so there's no way you could accidentally put them back on in the wrong place. If you unplug them you can set the module aside where
it's out of the way when servicing the burner. You will need to reconnect it if you want to perform any running tests, such as fuel pump pressure.
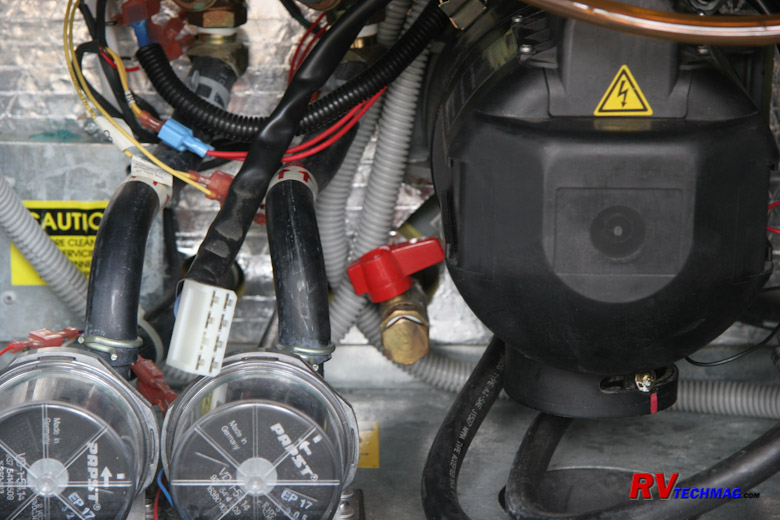
The boiler tank contains anti-freeze. A red handled drain valve is provided to drain that tank, which can be seen in this
image. I have found that this handle gets in the way when trying to remove the burner so I installed a 3/8" brass pipe lug in the end of the valve
so that antifreeze doesn't gush out all over the place whenever I bump the handle. The handle does need to be turned in order to access one of the
two eyebolts that hold the burner to the boiler assembly. One of these can be seen just to the top left of the burner assembly at the one o' clock
position on the image above this one. To remove the burner you'll need a 10mm deep well socket on a long extension to loosen the two nuts on those
eyebolts. You do not need to totally remove the nuts. Just back them off to the end of the threads and the eyebolts will swing off to the side. You
can then pull the burner free from the boiler housing and pivot it counter-clockwise one half turn to access the business end of the Webasto burner.
The air intake hose has also been removed in this image.
Servicing the Burner
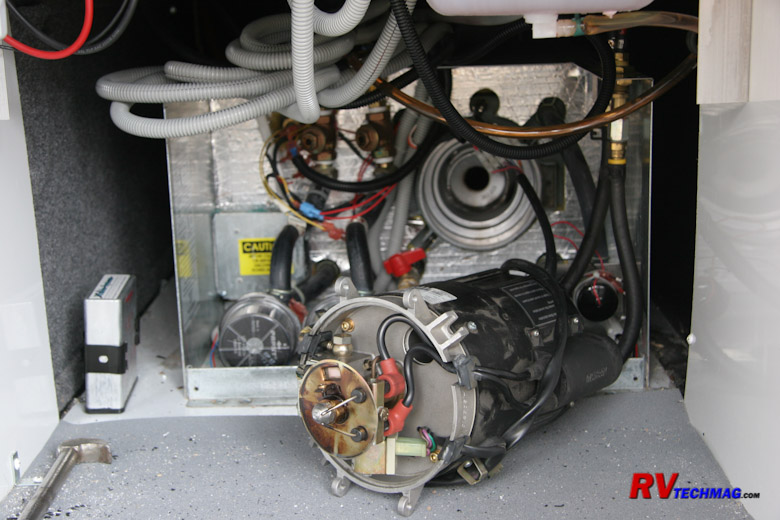
Once you have the eyebolts free you can rotate the burner and swing it out of the main enclosure. It is not necessary to
remove the fuel lines to perform this service. If you do, you will have some fuel dribbling to deal with. If you need to remove the burner for bench
testing or repair you will then remove the fuel lines from the swivel connections at the top-right of the enclosure. The aluminum swirler shown in
the boiler cavity is attached to a steel burner tube and can easily be removed by hand to inspect the boiler and clean if necessary. The two
electrodes are fed high voltage juice by the transformer to create an arc that will ignite the fuel spraying from the burner nozzle, which is the
silver object dead center in the burner. The round steel baffle is held to the nozzle holder casting via the black retaining ring, also visible.
This plate is free to float on the nozzle holder and will push tight against the swirler casting inside the combustion chamber as the blower fan
forces it forward. This ring must remain straight in order to seal off the airflow to the swirler. If the disc is distorted it can easily be bent
back by hand.
Electrode Adjustments
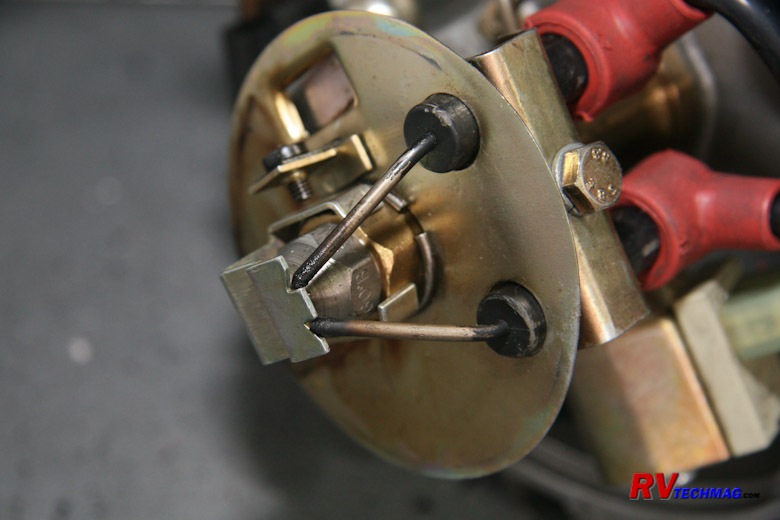
The electrodes need to be properly gapped and located. If the gap is too large the spark may not jump across the gap and your
burner will fail to ignite. If the gap is too small the spark may not be bright enough to ignite the fuel. Also, the gap needs to be placed just
outside the fuel spray cone so the electrodes need to be properly located in relationship to the nozzle. Fortunately an electrode gapping gauge is
supplied. Generally this unit is found attached to the side of the burner and can be used simply by removing the screw. If it was removed during the
last service and not replaced then you'll have to find where it was put or get another one. They are available online via the Aqua-Hot website.
To adjust your electrodes remove the nozzle from the nozzle holder and slip the tool over the nozzle holder. The tips of the
electrodes should rest in the notches that are cut into the gapping tool. If the electrodes do not line up, loosen the electrode retaining clamp bolt
and move them to the correct position. When tightening the bolt do not over tighten it or else you may bend the clamping bar or even crack the
ceramic insulator on the electrode. If that happens you will need to replace the electrodes. During most annual services you will not need to adjust
the electrodes. Once they are set in place they should stay put for a long time. Eventually the tips of the electrodes will erode away from the
constant arcing. When these tips appear to have widened the gap beyond 1/8" it is time to adjust your electrodes. If the gap is extreme you may need
to replace them.
Nozzle Replacement
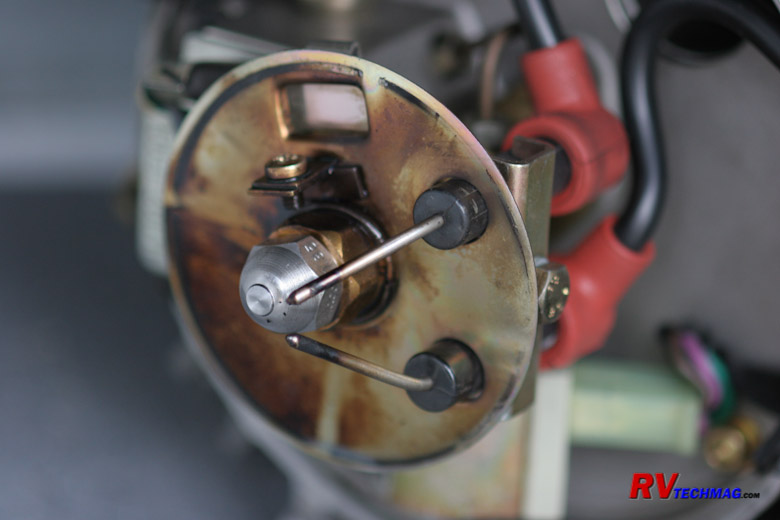
This is the number one service point on the Aqua-Hot/Hydro-Hot system. The nozzle is the most critical item on any oil-fired
burner. The nozzle itself is finely machined to spray a regulated amount of fuel in a pre-determined spray pattern. If even the smallest spec of dirt
enters the nozzle it can plug the vanes or orifice and cause it to spray in an erratic pattern so it is critical to deliver clean fuel to the burner
nozzle. It's also just as critical to use clean practices when servicing the burner and handling the nozzle. Do not touch the tip of the nozzle, drop
it, or allow dirt to get on the inlet screening. Even when kept clean, the nozzle will eventually wear out from the natural erosion of fuel as it
passes through the orifice. When that happens your burner will use extra fuel, resulting in a burner that runs rich and isn't properly atomizing its
fuel. You'll know that because it will have an unburnt fuel odor and may even be smoking. That's when it's time to replace the nozzle.
To replace the nozzle, place a 3/4" wrench on the nozzle holder to prevent it from turning. Then place a 5/8" wrench on the
nozzle and remove the nozzle by unscrewing it in a counter-clockwise direction. Carefully insert the new nozzle and tighten it using the two wrenches.
Once it is tight, back the nozzle off one quarter of a turn. Then, retighten it. This reseating of the nozzle is necessary to ensure that the threads
will properly seal and that no fuel will be leaking from the nozzle threads.
More Advanced Service Needs
If your burner is running well all it will need is a filter and nozzle change. However, if these have been changed and the
burner still is not running well, further testing and adjustment may be required. It can get very complex, and unless you want to do some serious
work and remove the unit for bench testing, you would be best off having it serviced by a professional. However, there are three items that you can
easily check to see if you need to go that far. These three areas are voltage, air intake, and fuel pressure.
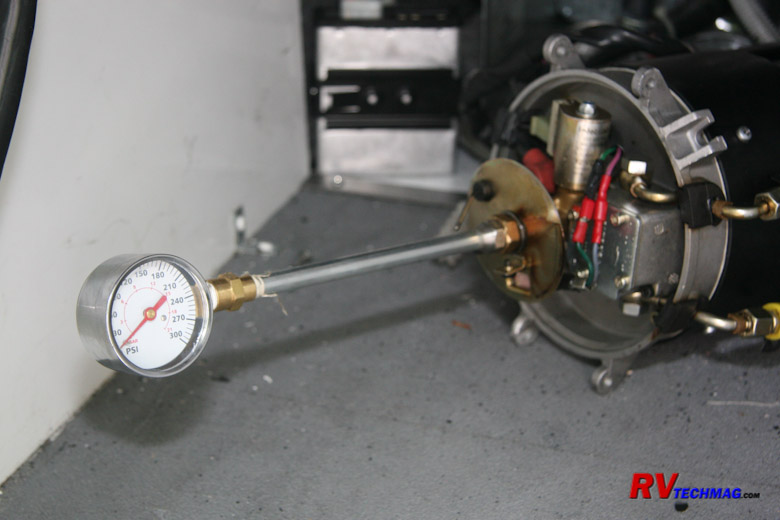
Fuel pressure is easy enough to check when you are servicing the burner. You do need to get a fuel pressure gauge to do this.
Aqua-Hot offers a fuel pressure gauge on their website. It's a bit on the pricey side, but then most Aqua-Hot items are. I chose to make my own gauge
and save some money. I did this by taking an old nozzle and drilling it out, tapping for 1/8" pipe threads, inserting a 1/8" pipe and air pressure
gauge with a 0-200 PSI range. That works just as well as the "official" gauge and saved me quite a bit of money. Even if you do need to purchase one,
it will be far less than paying a service tech to have to do this task for you so it is a good investment if you choose to perform your own
service work.
Regardless of whether you buy or make your own gauge, you will need one to be able to test fuel pressure. The gauge is inserted
into the nozzle holder so the nozzle is removed and the pressure gauge is put in its place. You will need to place the burner assembly on its side in
such a position so that you can see the gauge without handling the unit. When the fuel solenoid opens the ignition will create a high voltage spark
across the electrodes so you don't want to be handling the unit when that happens. You then switch on the diesel burner and watch the gauge. When the
burner first runs it will begin a purge cycle. During this time the blower fan will push air through the combustion chamber, purging it of any unburnt
fuel. After maybe 15-30 seconds the fuel solenoid will open, allowing fuel to flow through the nozzle. Once this happens the needle on the gauge will
suddenly swing over to the 145 PSI position. If your gauge shows 145 PSI, your pressure is correct and you can go and switch off the burner. It will
then enter another cool-down cycle whereby the blower fan continues to run before coming to a stop. Normally the fuel solenoid valve will engage
quickly and the fuel pressure will rise smartly. The same holds true upon shutdown but when the pressure gauge is connected the fuel will be locked
inside the tube with no way to bleed out so your gauge will not return to zero as fast as it rose. In fact, you may need to loosen the threads in
order to bleed off the pressure locked up inside the gauge assembly.
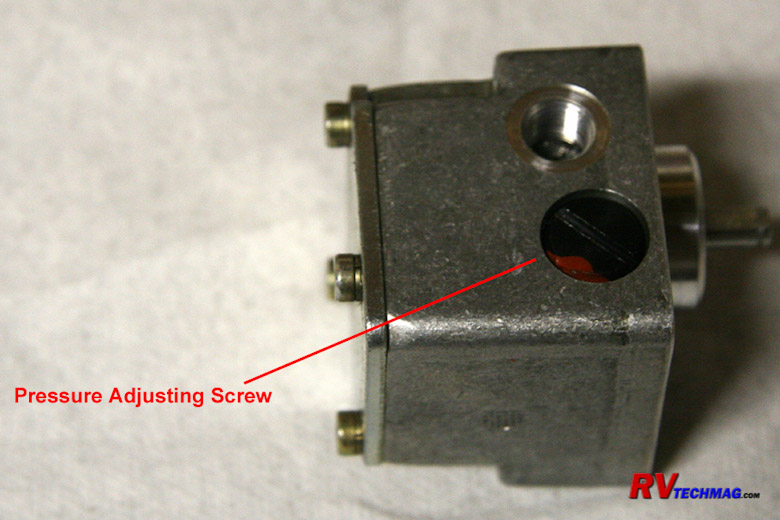
If the pressure needs adjustment there is a small screw on the side of the fuel pump that can be turned to adjust the fuel
pressure delivered to the nozzle. You only need minute adjustments to bring it to 145 PSI so take it easy when performing this. You'll need to do
this while the burner is running so you will need to remove the high voltage wires from the electrodes or transformer in order to prevent voltage
from jumping around and giving you a really good sting. If the pressure is not coming into tolerance or is gradually dropping when running you'll
have other issues that will need to be dealt with. You may be sucking air into the fuel lines, you may have a bad fuel pump strainer screen, or a
bad fuel pump. Either way it's time for some higher level service. You'll need to refer to the service manual or have it dealt with by a
professional at that point.
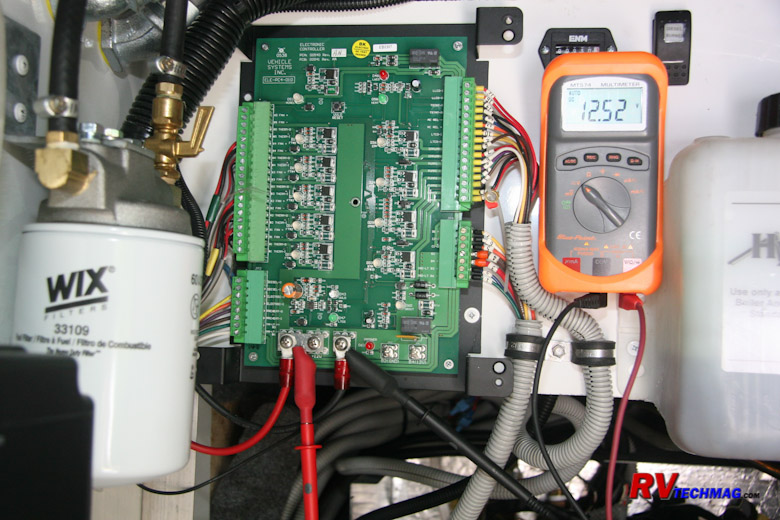
Your Aqua-Hot system needs to have adequate voltage present. If the voltage is low your burner motor will run slow. If that
happens you won't get enough airflow through the chamber to provide clean burning and your fuel pump may not develop full pressure due to lower RPM.
To check for proper voltage take the leads from a voltmeter and test for adequate voltage at the hot terminal on the controller board. The Aqua-Hot
requires voltage between 11.5 and 14.0 volts DC.
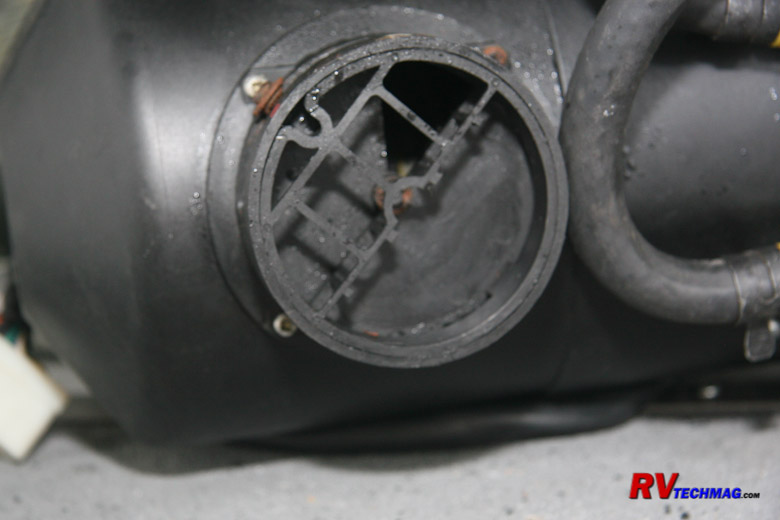
Any flame requires both air and fuel in order to burn. To have a clean burning flame you need to have the proper ratio of air
to fuel. Your Aqua-Hot diesel burner is no different. The air intake tube attaches to the base of the burner. The base includes a baffle that can be
rotated to increase or decrease the size of the air intake port. The baffle is held in position by a small Phillips head locking screw. When fully
open, the port will be one half of circle, in other words 180 degrees. It is possible to fully close the opening but not possible to open it more
than 180 degrees. The systems are generally preset at the factory to a 90 degree opening, which is the middle of the adjustment. Sometimes this can
vary and you may find a red stripe that marks the position of the baffle adjusting screw for its initial opening position. If you open this up
farther you will get more air and if you reduce the aperture you'll get less air. In order to properly adjust this opening you will need some
sophisticated exhaust gas sampling equipment, which is covered in the service manual but is beyond the scope of this tutorial. For all practical
purposes just leave it alone.
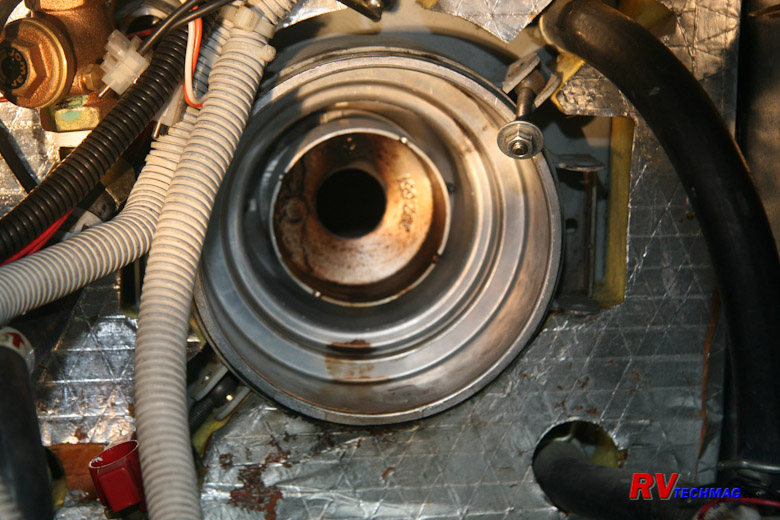
The combustion chamber consists of an aluminum swirler and a steel tube. This unit slides into the boiler cavity and is easily
removed by hand once the burner motor has been removed.
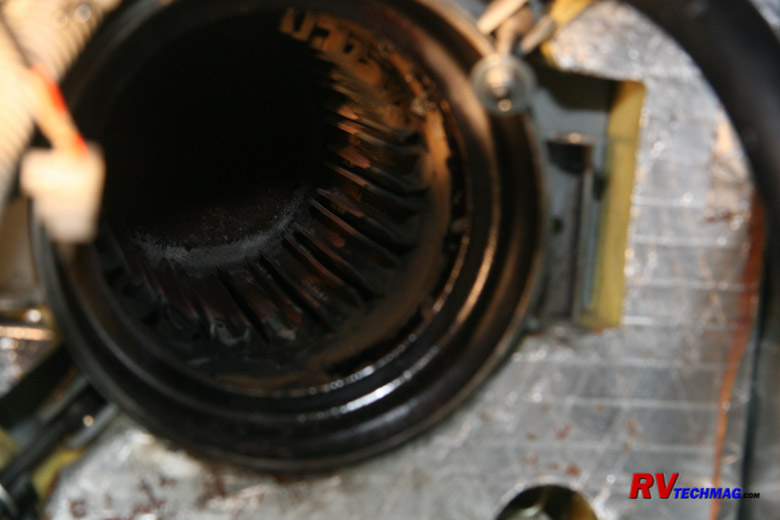
Once the combustion chamber has been removed the boiler housing should be checked for any build up of soot. A wire brush and
shop vacuum are helpful in cleaning the chamber to restore it to peak efficiency.
Reassembly
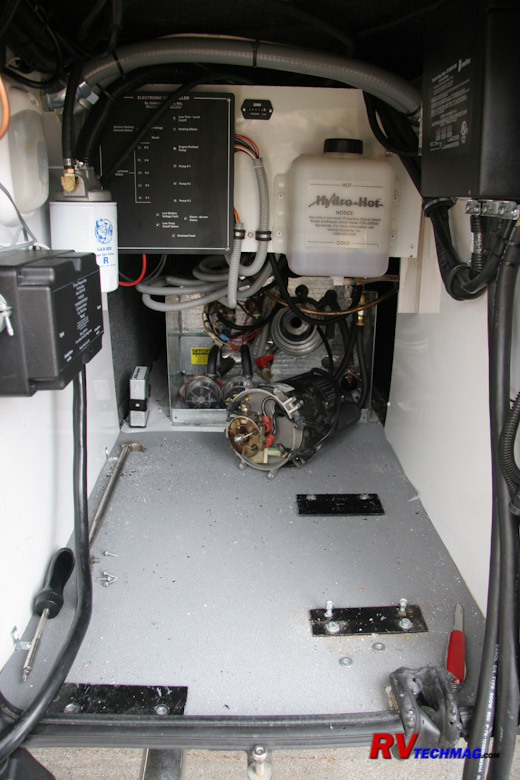
Once you have every thing taken care of it's now time to reassemble your unit. Rotate the burner assembly and place it in
position against the boiler assembly. If you have previously removed the combustion chamber tube and swirler, be sure to reinstall it prior to
reconnecting the burner. Swing the two eyebolts off to the side and press the burner motor up against the mounting lugs. Drop the eyebolt nuts
down over the burner motor mounting lugs and carefully tighten. Be sure to hold the burner up tight against the boiler with one hand and use a
socket and extension, but no ratchet at this time, to hand tighten the retaining nuts evenly. Once you have them snugged up by hand, add the
ratchet and tighten them down. Be careful to not over-torque the eyebolt nuts or else you may break the aluminum lugs off of the burner casting,
resulting in a very expensive replacement cost. Once you have the burner installed, reattach the air inlet hose to the burner and test run the
unit. If everything is working fine and there are no leaks or other issues, reinstall the sheet metal access cover and put together your basement
compartment and you are all done.
A Fix for One Common Problem
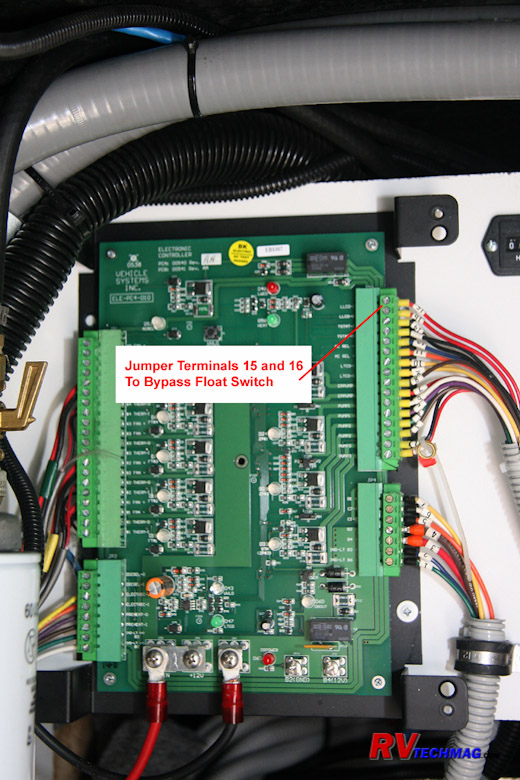
The Hydro Hot boiler contains a float switch to monitor the level of the boiler antifreeze. If the antifreeze level drops
below a given point, the float switch will open the circuit to the controller board and will shut off both the diesel burner and the electric heating
element. This float switch has been known to gunk up and stick in the open position. You may have plenty of antifreeze in your boiler but the
switch doesn't think so and prevents the unit from heating. If you are traveling and suddenly find that you have no heat check the control panel.
If it indicates low boiler antifreeze level check you antifreeze. If there is plenty there in the plastic surge tank then you undoubtedly have a
failed float switch.
Fortunately there is a temporary fix to restore your heat until you can get the float switch replaced. By removing the 4
screws on the controller panel's cover you will expose the main circuit board. At the very top-right are two wires in a connector plug. These wires
are numbered 15 and 16 and go to the float switch. By loosening these two screws you can removed the float switch wires and insert a small jumper
wire. That will restore the ability to reheat your boiler. Note that by doing this you are bypassing a safety option so be sure to keep an eye on
the antifreeze level and have the float switch replaced as soon as it's convenient.
Summary
Servicing your own Aqua-Hot system isn't all that bad as long as you have some time on your hands, and don't have any major
problems to deal with. You can save some serious labor costs, and gain the satisfaction of another job well done. If your unit is smoking or has
obnoxious odors it may need more than this basic service. It may be time to call in a professional if these issues still remain after you have
performed the basic service. If you still want to continue, be sure to read the appropriate shop manual for your system and follow the
troubleshooting flowcharts to see where the problem may be.
Source
Aqua-Hot
(800) 685-4298
www.aqua-hot.com
Return to Home Page
If you enjoyed this article be sure to recommend RVtechMag.com to your friends, like us on Facebook or Twitter
or subscribe to our RSS feed.
|