Building an Entegra Coach
Following the Construction of a 2016 Cornerstone from Start to Finish
Article Date: January, 2016
Article and Photography by Mark Quasius
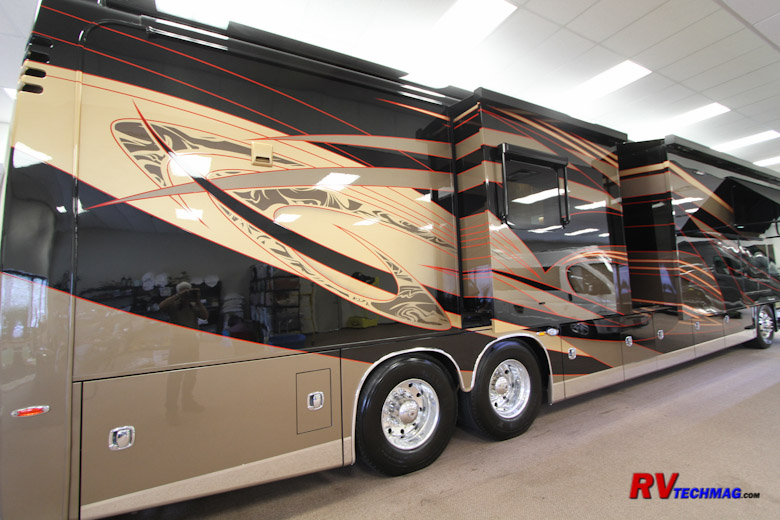
Entegra Coach has developed a reputation for building motorhomes that offer high quality and innovative design.
In fact, owners of Entegra Coaches are some of the most loyal customers within the RV industry and very proud of their coaches. I was
recently given the rare opportunity of being allowed to follow and document the construction of our new 2016 Entegra Cornerstone from
start to finish and this article will give you an idea of how Entegra's are built and what really makes up an Entegra Coach. If you walk
into a new Entegra Coach at a show you will see a well built coach but much of what truly makes an Entegra Coach what it is cannot be seen
at first glance. You have to look deeper into the construction so hopefully this article will give you a better understanding of just how
an Entegra Coach comes together and what sets it apart as truly unique.
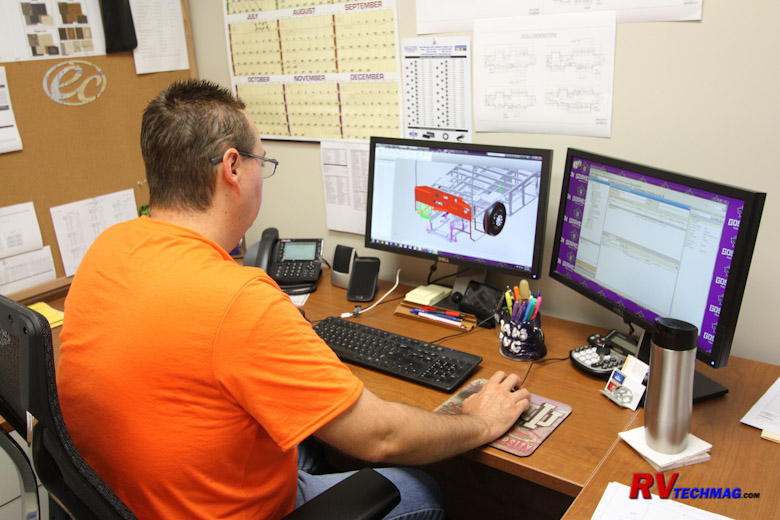
Like most coach manufacturers, Entegra begins with the design process. The engineering staff uses CAD systems to
lay out the floorplan and engineer all of the components that will be used in this particular model. The supporting framework is designed
into the chassis and every bracket and fastener is specified. At the same time, the engineering staff will be
designing the electric
system and wiring harness and plumbing systems. After the designs have been completed a prototype unit is built and the various sales,
engineering and production departments weigh in and determine if any changes need to be made before beginning production.
The Chassis
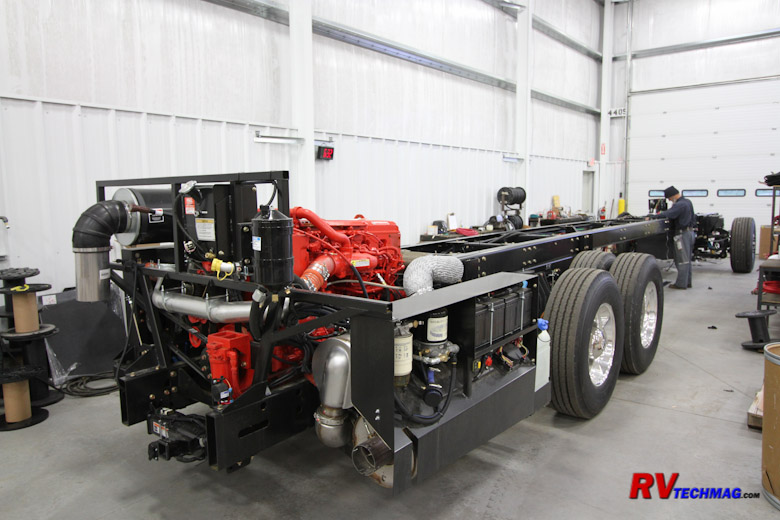
The bare chassis arrives from Spartan Chassis and is unloaded at the rear of the main assembly plant. The chassis
then enters the building and is prepped. This stage involves running the battery cables, hydraulic jack lines and other items now while
it is easy to access before all of the welding is done.
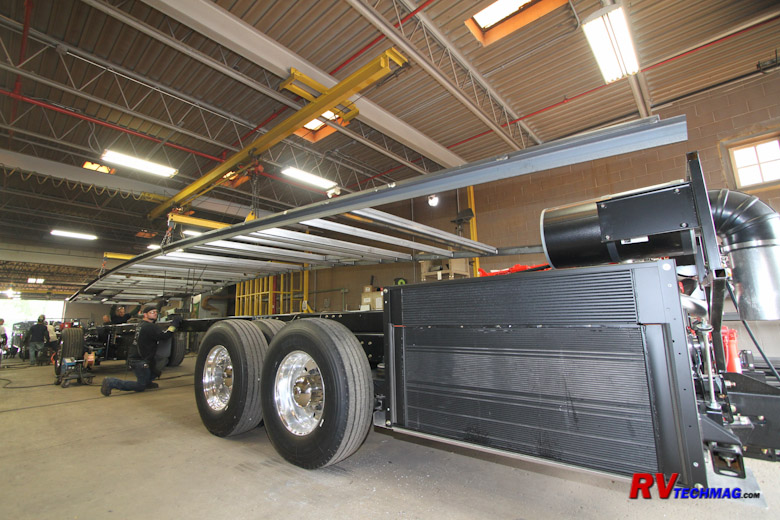
The sub-floor structure is created in a jig and then lowered onto the chassis.
|
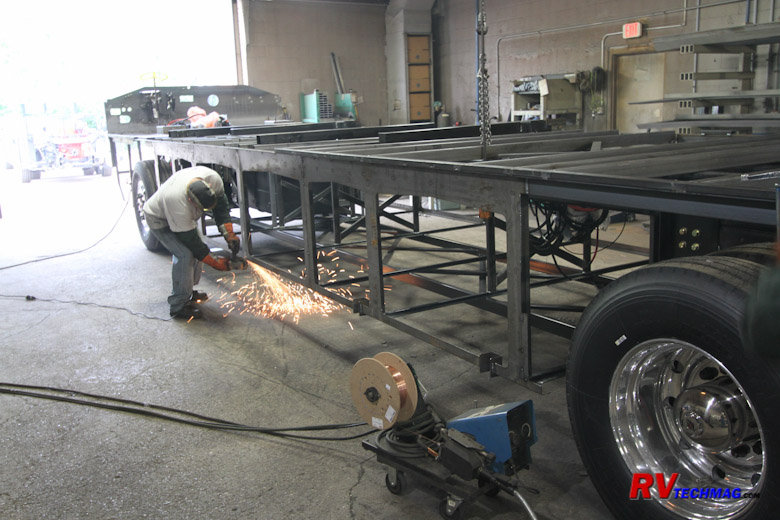
The framework for the basement compartments and the diagonal bracing is welded in place and all weld joints are
ground down.
|
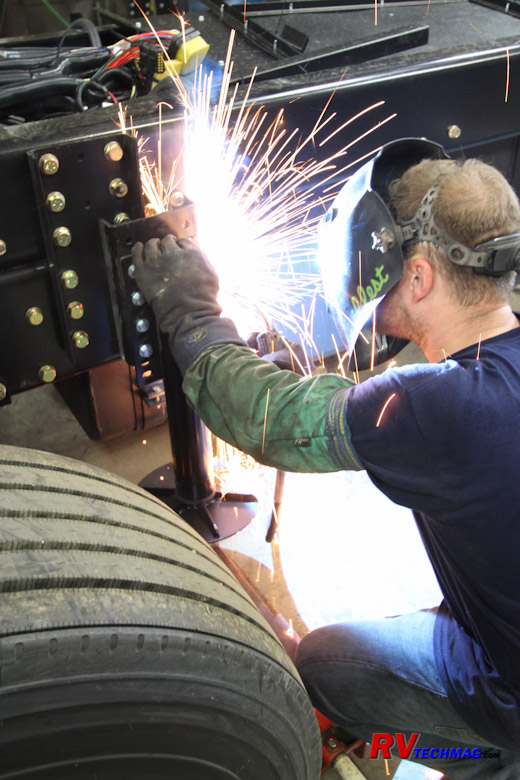
The mounting plates for the Equalizer leveling jacks are welded into place after the jacks have been bolted to the mounts
to ensure proper jack alignment.
|
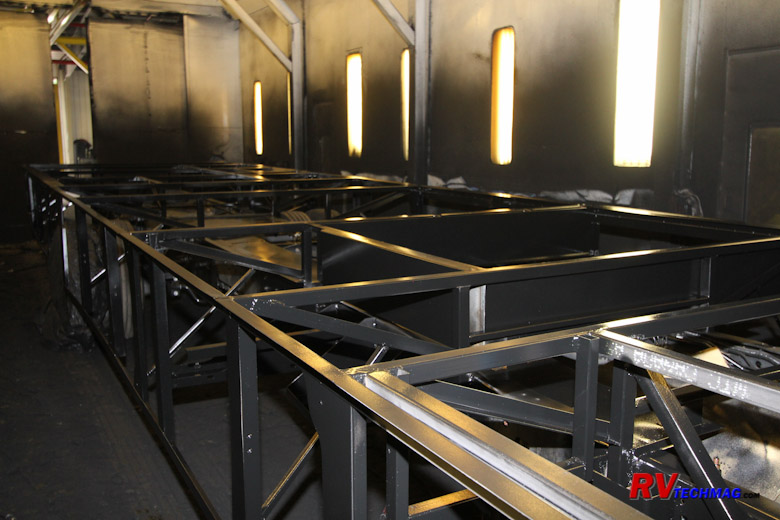
The last step is to paint the newly welded chassis to prevent any rust or
corrosion.
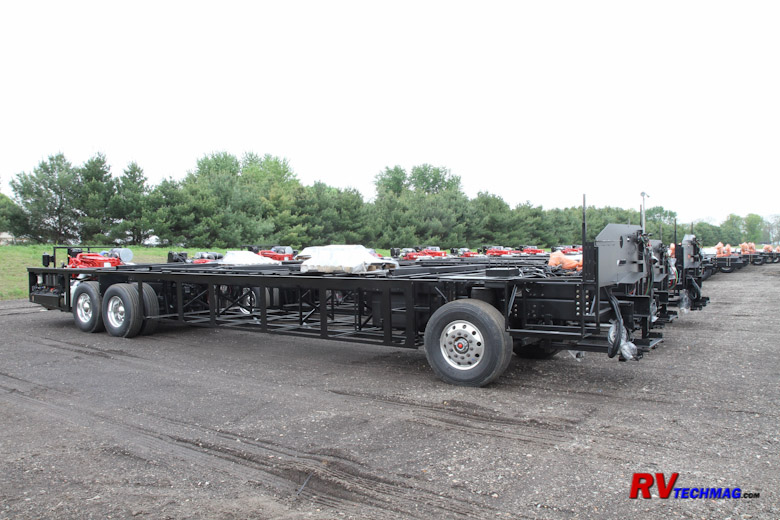
After the welding is completed the chassis is parked at the rear of the assembly plant, ready to begin construction.
|
The chassis then goes to the weld shop. At this point the steel sub-structure that supports the coach is built and
welded to the chassis frame. The hydraulic leveling jacks are added, a bulkhead is installed, the generator mounting system is added and
the diagonal X-bracing is added. This X-bracing is added both vertically and horizontally and is a major
contributor to Entegra's
reputation for an excellent handling motorhome. This minimizes flex in the chassis and allows the suspension to do its work more
effectively. This also creates less stress on the superstructure of the motorhome, which eliminates the squeaks and groans that can occur
over timer when the coach body flexes during travel.
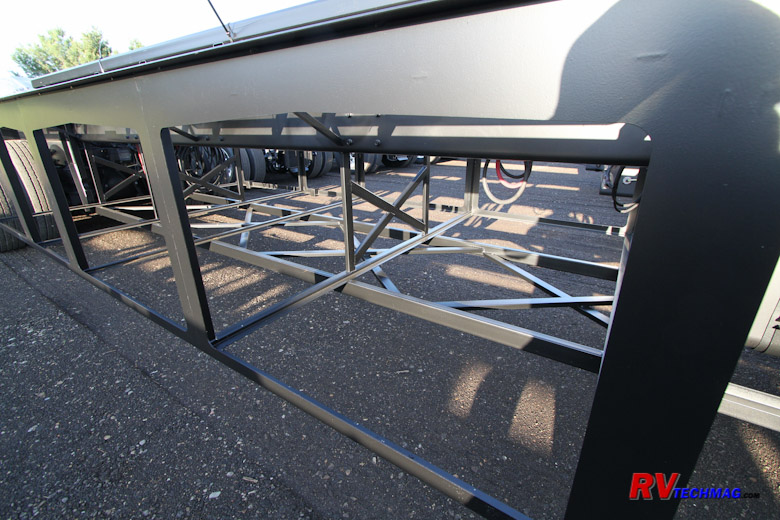
The finished chassis, showing the X-bracing that contributes to Entegra's ride and handling.
At this point the chassis is returned to the main assembly plant where it will spend the next three weeks as
it progresses down the assembly line. Entegra's new 135,000 square foot plant was launched in April of 2015. This coach is actually the first
Cornerstone to be built in this state of the art facility. The coach is driven into the first bay where the initial steps are taken, which
include installing the primary wiring harnesses, generator, batteries and other major components.
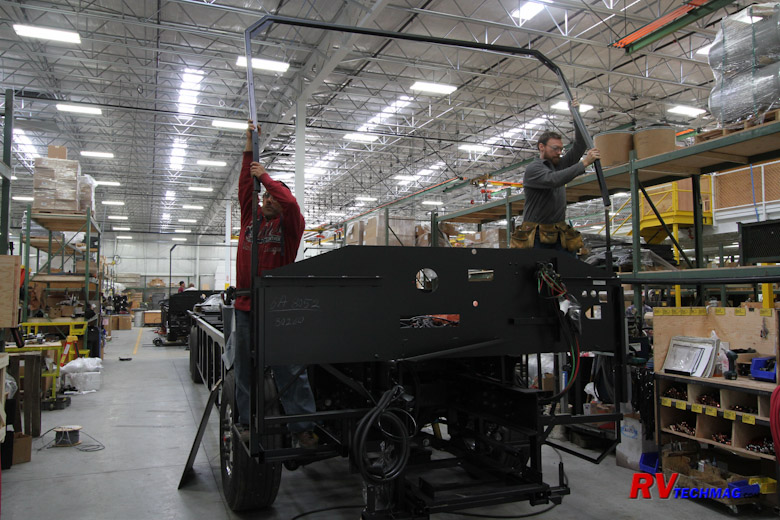
A steel roll bar style hoop is added to the front of the chassis to
afford additional occupant protection in the
cockpit area as well as eliminating any flexing that could cause stress in the windshield area.
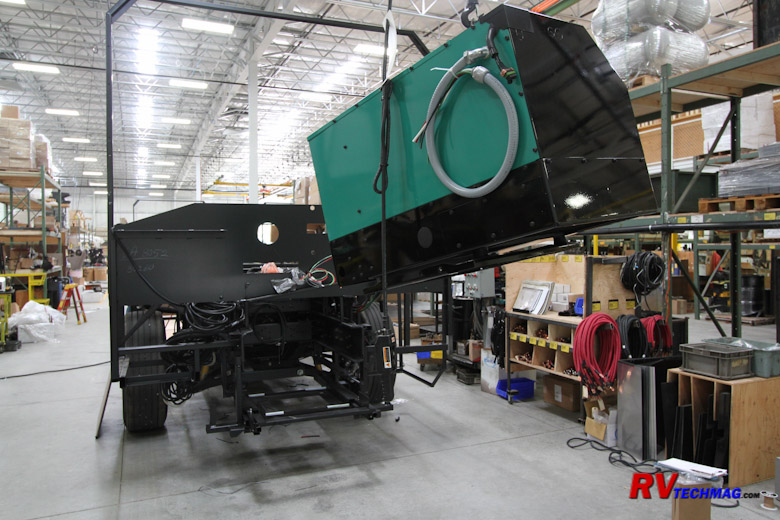
The 12,500 watt Onan generator is installed into the chassis via an overhead hoist.
|
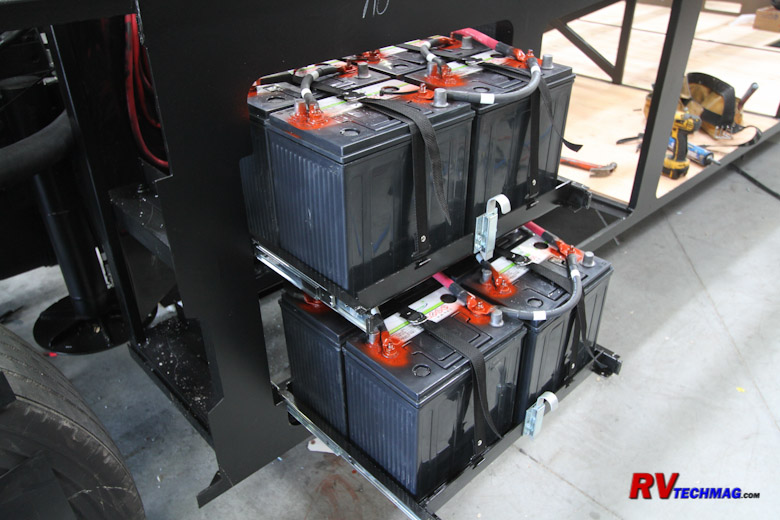
A bank of eight AGM batteries is added to a pair of slide-out battery trays for ease in service access. Circuit breakers
and fuses are installed and the batteries are connected to the system.
|
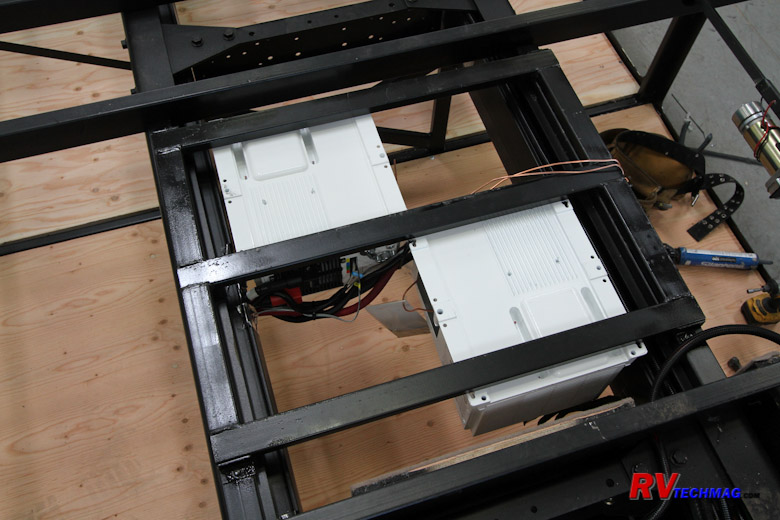
A pair of Magnum true sine wave inverters are mounted into a steel frame which is lowered into a space between the
frame rails so as to not intrude on any basement cargo storage space.
|
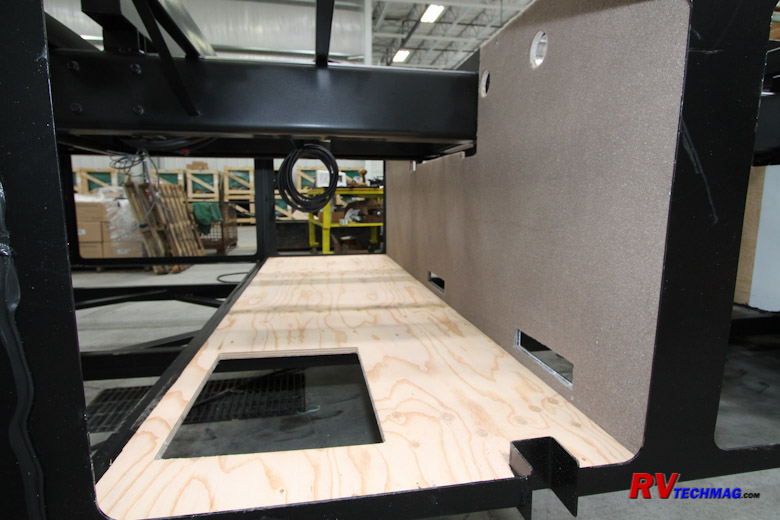
The basement compartments are fitted with plywood floors and walls.
|
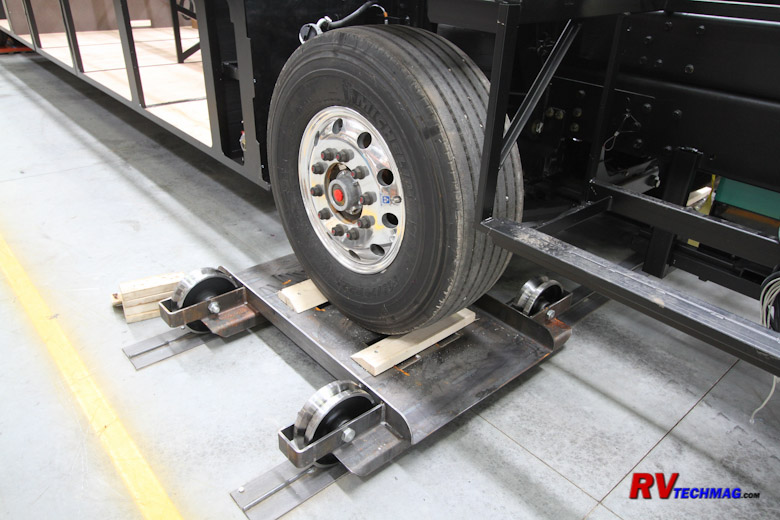
The coach is then rolled back to the main assembly line. The front tires of the coach are placed on tracked
dollies while the rear axles are placed on pneumatic hover pads that will move the coach laterally from station to station as it
progresses down the 30+ stations in the plant.
Return to Home Page
If you enjoyed this article be sure to recommend RVtechMag.com to your friends, like us on Facebook or Twitter
or subscribe to our RSS feed.
|